Manufacturers in the medical technology industry operate in a field characterized by the highest quality demands on their products, high throughput rates, and strict documentation requirements for their manufacturing processes. Kistler supports these companies with new and proven solutions for automated process monitoring and seamless quality assurance.
Measurement technology for efficient process optimization and quality assurance in medical technology
Winterthur, May 2025 – At automatica 2025 (June 24 to 27 in Munich, Germany), Kistler will be presenting a broad product portfolio for automated manufacturing processes – or those on the way to being automated –at booth 205 in hall B5. Among other things, innovations for the manufacture of medical technology and pharmaceutical products will be on display. Visitors can experience these newly developed solutions live – including the high-speed joining module NCFQ 2166A, the new maXYmos BL 5867C process monitoring system, as well as software tools for compliant documentation, intuitive reporting, and data-driven process optimization.
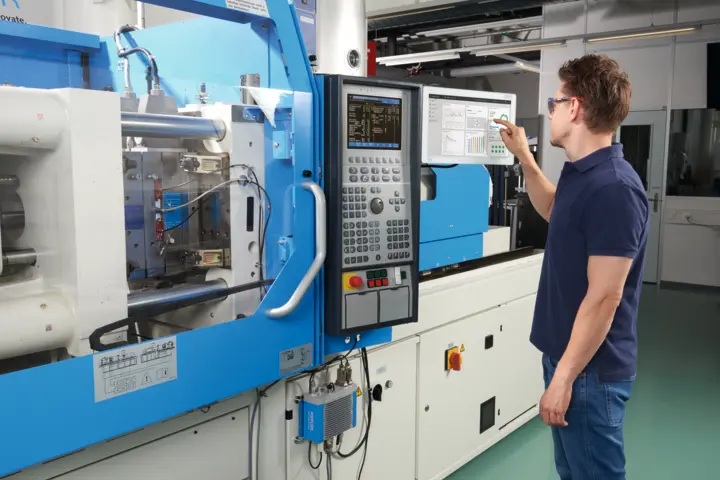
Premiere at automatica 2025: High-speed joining module with acceleration compensation
The new NCFQ 2166A high-speed joining system will celebrate its premiere at automatica 2025. In this compact system, Kistler combines the dynamics of electromagnetic linear modules with the precision of piezoelectric measurement technology. With acceleration of up to 50 m/s², speeds of up to 5 m/s, and integrated acceleration compensation, the module is particularly suitable for highly dynamic joining applications with small forces of up to 500 N, for example in the assembly of autoinjectors. It is also used in other areas of medical technology, and in electronics and semiconductor manufacturing, where high dynamics meet maximum measurement precision. The system is accompanied by the maXYmos NC 5847B process monitoring and control system. Optional acceleration sensors in conjunction with the ICAM 5073B industrial charge amplifier enable automatic acceleration compensation for the first time. They allow sole joining forces to be determined – and thus greater process reliability and control under highly dynamic conditions.
Smart Single Stations facilitate process development
With the second generation of Smart Single Stations (SST), Kistler offers companies a turnkey solution for demanding joining and testing processes in development and manufacturing. It enables maximum precision and full traceability and can be individually tailored to the respective application, whether it is a manual workstation or a fully automated manufacturing cell. During development, the flexible tool holder and integrated configuration management enable processes to be developed and validated in advance with ease. The compact station, which will be on display at automatica 2025 with an NCFH joining module (60 kN), is suitable both as a stand-alone solution and for modular lines.
Automated process monitoring with maXYmos BL 5867C
The maXYmos BL 5867C process monitoring system will also be on display at automatica 2025. It is specifically designed for reliable quality assurance in joining and pressing in the medical technology, automotive, electrical, and electronics industries. In these automated processes, maXYmos BL evaluates up to ten processes per second. The user intuitively configures the evaluation basis via the large, high-contrast touchscreen. The process monitoring system allows system integration via industrial Ethernet using common protocols EtherCAT, PROFINET, and EtherNet/IP. Via OPC-UA, maXYmos BL can also be integrated into the IIoT manufacturing environment for comprehensive parameter access. In terms of evaluation, user management, and digital interfaces, this new generation is similar to the even more powerful maXYmos TL, thereby simplifying the operation of both device classes in mixed systems.
KVC 821 for automated quality assurance at the end of the production line
The KVC 821 optical inspection system handles automated quality assurance at the end of the production line. Thanks to its eight cameras, the integrated Multicapture Device enables high-resolution inspection images of the entire surface of the workpieces without the need for mechanical rotation. The additional 2.5D and 3D measurements and the subsequent precise evaluation of the inspection images by Kistler's proprietary KiVision software reliably detect scratches, dents, and dimensional deviations. Depending on the number and scope of the inspection requirements, the system achieves cycle times of up to 800 parts per minute. Kistler also uses artificial intelligence to detect previously unknown or rare anomalies. The measured values can be imported directly into software, which evaluates and visualizes them statistically.
Software solutions for process monitoring and control in plastics manufacturing
In the production of medical devices, strict tolerances for the processing must be maintained. To keep efficiency in plastics manufacturing at a high level, Kistler offers the ComoNEO process monitoring system, a solution for the continuous monitoring and control of injection molding processes. The data from the in-mold pressure measurement technology installed in the mold can also be used for process
optimization. ComoNEO predict analyzes the collected process data using AI to make quality predictions for individual products and to minimize scrap. ComoNeo MULTIFLOW regulates cavity filling evenly, fully automatically, and quickly, even during process fluctuations. This reduces quality assurance costs to a minimum and avoids (pseudo) scrap as well as expensive downstream inspection costs.
AkvisIO IME (Injection Molding Edition): Analyze and evaluate process data
The AkvisIO IME (Injection Molding Edition) process data analysis software performs further comprehensive process data analysis and statistical evaluation in injection molding manufacturing. It can be connected to Kistler process monitoring and control solutions such as ComoNeo and ComoScout. The software analyzes process and machine data using classic statistical methods and artificial intelligence with a focus on quality. Communication standards such as the Ethernet-based Euromap 77 make the machine itself a data source and AkvisIO the single source of truth for reliable production data. When used in medical technology, the software thus helps to fulfill the industry's detailed documentation requirements.
jBEAM software enables digital process optimization and automation
Kistler also offers a solution for the final step in manufacturing at automatica 2025: with the help of jBEAM software solution, users can automatically generate the exact reports required in the medical technology industry. The standard-compliant report can be compiled according to specifications or standard sheets using drag & drop. Changes to the specifications can be implemented quickly and without programming knowledge.
The software also helps to automate the manufacturing processes themselves. Kistler's solution collects and filters measurement and process data from the entire shop floor, development, and testing, globally if required, and prepares it according to the requirements of different departments and users. This provides users with a basis for decision-making during process optimization and automation or for continuing ongoing automation projects. Kistler will demonstrate the versatility of the application on site, as visitors can bring their own process data. Kistler experts will evaluate it at the booth and then advise on the optimization and automation potential of the analyzed process.